Совсем недавно мы рассказывали о достоинствах и недостатках керамических тормозных колодок. Однако керамическими в тормозах могут быть и диски. На самом деле они многокомпонентные, но это не так уж важно. Важно другое: правда ли эти диски так хороши, что за них иногда не жалко заплатить и 500 тысяч рублей, и 800, а в некоторых случаях – и целый миллион? Обоснованы такие траты или можно купить что-то подешевле?
Первые тормозные диски появились более ста лет назад и были призваны заменить механизмы барабанного типа. В 1902 году Уильям Ланчестер предложил конструкцию, внешне похожую на дисковые тормоза некоторых современных велосипедов. Изобретение показало себя неплохо, но металл, который в них применялся – как правило, медь – очень сильно скрипел. А самое главное – они сильно нагревались, что приводило к быстрому закипанию используемых на тот момент тормозных жидкостей на основе спиртов и масел. Из-за подобных недостатков внедрение их на автомобилях отложилось до середины века.
К началу 1950-х годов значительно выросла мощность моторов легковых машин, а конструкция подвесок и рулевого управления стала более совершенной. Все это позволило ездить достаточно быстро, но вот барабанные тормоза за такими скоростями уже не поспевали. Именно тогда инженеры снова вернулись к дисковым тормозным механизмам. Точнее, опыты с ними они вели непрерывно, но по-настоящему работоспособной и не очень сложной конструкции за это время создать так и не получилось. Однако в результате упорного труда в компании British Girling все же появились качественные дисковые тормоза современного типа. Впервые они были установлены на дорогой и быстрый Jaguar C-Type.
Несмотря на то, что новая разработка оказалась более жизнеспособной, некоторые недостатки нашлись и у нее. Например, при неудачном сочетании колодок и дисков новые тормоза скрипели так же, как и раньше. Кроме того, сами сопрягаемые детали изнашивались гораздо быстрее, чем у барабанных тормозов. Последние, кстати, поэтому так и не утратили актуальности: их до сих пор еще можно встретить на недорогих и не очень мощных автомобилях.
На грузовых автомобилях барабанные тормозные механизмы не сдают своих позиций и до настоящего времени. Дело в том, что бесконечно увеличивать размеры дисков и колодок для эффективного торможения невозможно: их ограничивают габариты колеса. Зато в барабанных механизмах это легко можно сделать, увеличивая ширину колодки и внутренней поверхности барабана – размер колеса тут не имеет особого значения. При этом, что важно, хорошая эффективность достигается довольно бюджетно.
Первые тормозные диски изготавливались из чугуна и были цельными. Даже для мощных автомобилей того времени этого оказалось вполне достаточно. Но, как известно, прогресс не стоит на месте, и лошадиных сил в моторах становилось все больше, а максимальная скорость увеличивалась. И со временем снова возникла проблема с остановкой автомобиля с большой скорости: тормоза работали хорошо ровно до тех пор, пока не перегревались колодки с дисками. А перегревались они быстро.
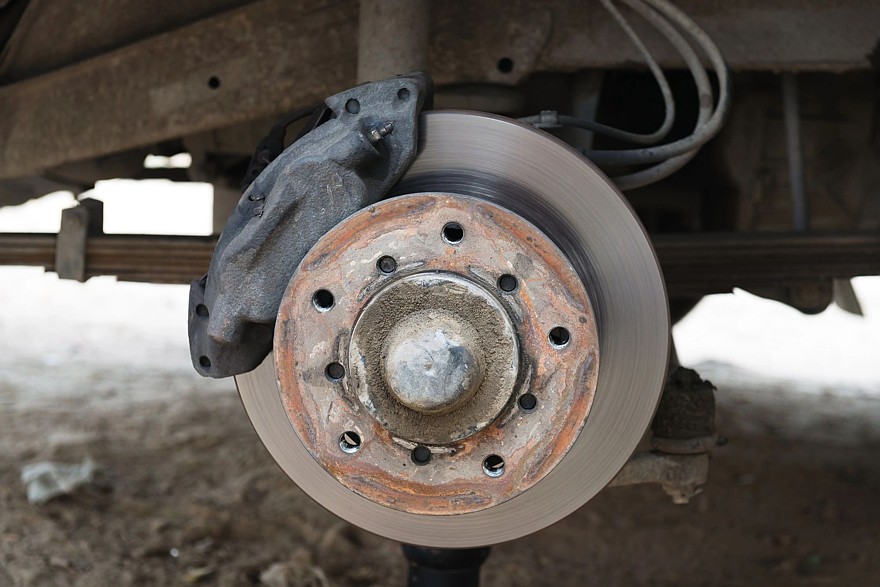
Инженеры нашли выход: для лучшего охлаждения в тормозных дисках между двух его плоскостей они сделали воздушный зазор. Соединялись плоскости большим количеством изогнутых перемычек, которые при движении благодаря своей форме усиливали воздухообмен. Так появились вентилируемые тормозные диски. Однако существовала и еще одна проблема – засорение сопрягаемых поверхностей продуктами износа. Тогда в рабочей плоскости стали делать отверстия – перфорацию. Через эти отверстия эффективно удалялись не только твердые продукты износа, но и газы, образующееся при нагреве тормозных колодок. Позже для этого же стали делать и проточку – нанесенные через определенное расстояние пропилы на рабочей поверхности диска.
Казалось бы, на этом можно было и остановиться. Но того, чего хватало даже самым мощным гражданским автомобилям, все же недоставало гоночным. Особенно – в королевском спорте, в Формуле 1. Тормозной диск на спортивном автомобиле, даже хорошо вентилируемый, перегревался в ходе гонок очень быстро. Ряд циклов интенсивных нагревов и последующих очень эффективных охлаждений приводил к тому, что его попросту вело – рабочие плоскости деформировались, вследствие чего качество торможения опускалось до неприемлемого опасного уровня. Немаловажным моментом был и тот факт, что для улучшения работы тормозного диска требовалось увеличение его габаритов, как диаметра, так и толщины. Это приводило к росту неподрессоренных масс, а также к невозможности разместить весь механизм необходимого размера на оси.
Первоначальным решением стало изготовление составных тормозных дисков. Благодаря использованию металлов с разными температурными коэффициентами удалось сохранить габариты тормозных механизмов в разумных пределах и не слишком сильно увеличить их массу. Внешнюю часть, как и прежде, изготавливали из чугуна, который имеет хорошую твердость и относительную стабильность при работе, а внутреннюю – из легкого сплава, чаще всего – алюминия. Одним из вариантов таких составных вариантов являются плавающие тормозные диски, где части не имеют жесткого соединения.
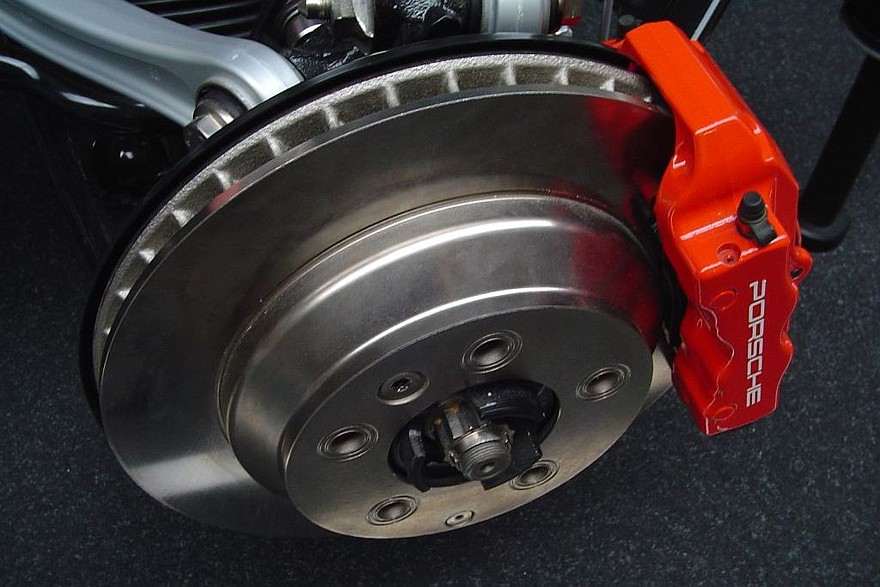
Но и этого со временем стало не хватать. Запас возможностей металлов был уже исчерпан, и пришлось искать другие материалы. Первые композитные тормозные диски, состоящие из керамических частичек, армированных углеволокном, были спроектированы инженерами Alstom для компании TGV в 1988 году. Но разрабатывали их не для автомобилей, а для скоростных поездов. Эти диски изготавливались по технологии CMC (Ceramic Matrix Composites), которая предполагает соединение армирующих волокон с керамической матрицей.
Новая технология показала отличные результаты на железных дорогах и довольно быстро распространилась на автомобильный транспорт. Буквально в течение года у Porsche появилась первая модель с керамическими тормозными дисками – 911 Turbo S. Правда, тогда их предлагали исключительно в виде опции. В 1990-е годы появились модели престижных брендов, оснащенные керамическими тормозными дисками в базовой комплектации. Однако массовыми такие тормоза не стали, и даже спустя десятилетия их устанавливают далеко не на все дорогие автомобили, и зачастую они доступны лишь за доплату.
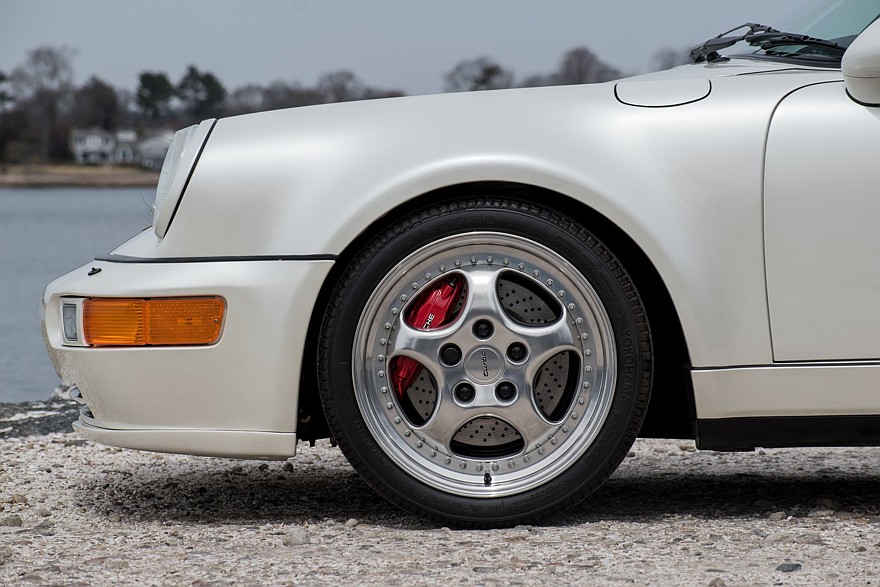
Преимуществом керамических тормозных механизмов в сравнении даже с лучшими составными являются способность выдерживать более высокую рабочую температуру без потери качества торможения, снижение до 50% массы при аналогичных габаритах, больший срок службы и сохранение параметров в течение этого времени. Кроме того, они совершенно не подвержены коррозии.
В настоящее время керамические диски производят по технологии CCM (Carbon Ceramic Matrix) из композитного материала на основе углерода и керамики. Базой служат армирующие наполнители, как правило – углеродное волокно, которое смешивается с одним из нескольких полимеров (полиамидом, полиэтиленимином, полиакриламидом и другими). Готовую смесь запекают при высокой температуре в форме в течение нескольких часов. В итоге вокруг волокон формируется полимерная матрица. После охлаждения заготовки поверхность обрабатывается на высокоточных станках с одновременным сверлением необходимых отверстий. Затем будущий тормозной диск нагревается до температуры в 1000 градусов и подвергается ее воздействию в течение суток. После этого температуру повышают еще на 500 градусов и добавляют к заготовке мелкодисперсный порошок кремния, который взаимодействует с углеродным остатком. На завершающем этапе происходит финальная обработка тормозного диска. Некоторые типы дисков проходят еще одну финишную полировку.
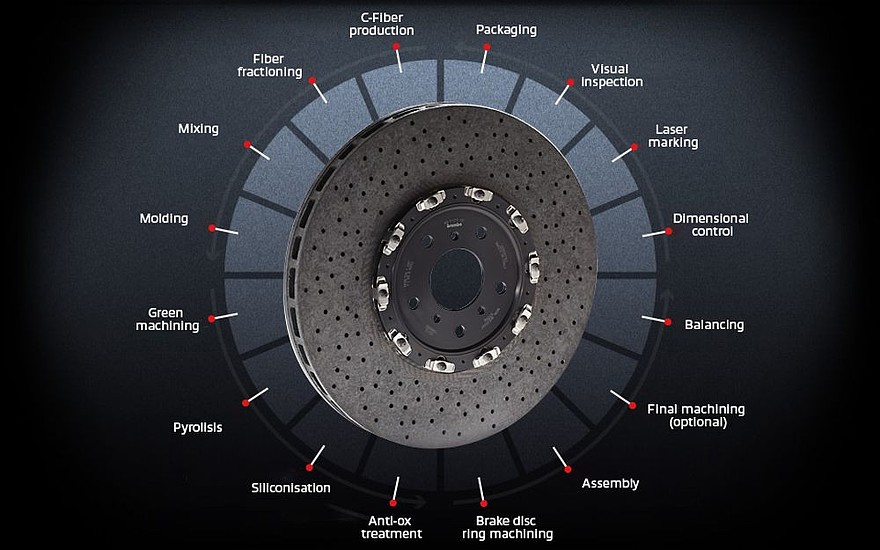
Процесс изготовления керамического тормозного диска длительный и состоит из множества операций. Из-за этого его стоимость получается весьма значительной, что, пожалуй, является одним из самых серьезных недостатков керамических дисков. Кроме того, к небольшим минусам можно отнести хрупкость: эти диски не терпят ударов. При этом механическое повреждение не всегда заметно сразу и может проявиться только во время эксплуатации. Поэтому аккуратное обращение с керамическими тормозными дисками обязательно.
Интересный факт: при том, что на тяжелых грузовиках не сдают свои позиции барабанные тормоза, на них же начали появляться и карбоновые тормозные диски. Да, это совсем не дешево, но в некоторых условиях оправдано. Например, если большегрузы двигаются по горной местности: керамические тормоза могут длительное время работать при высокой температуре на затяжных спусках. В любом случае стоимость автомобиля и груза, который он перевозит, несоизмеримо выше цены даже таких дорогих механизмов.
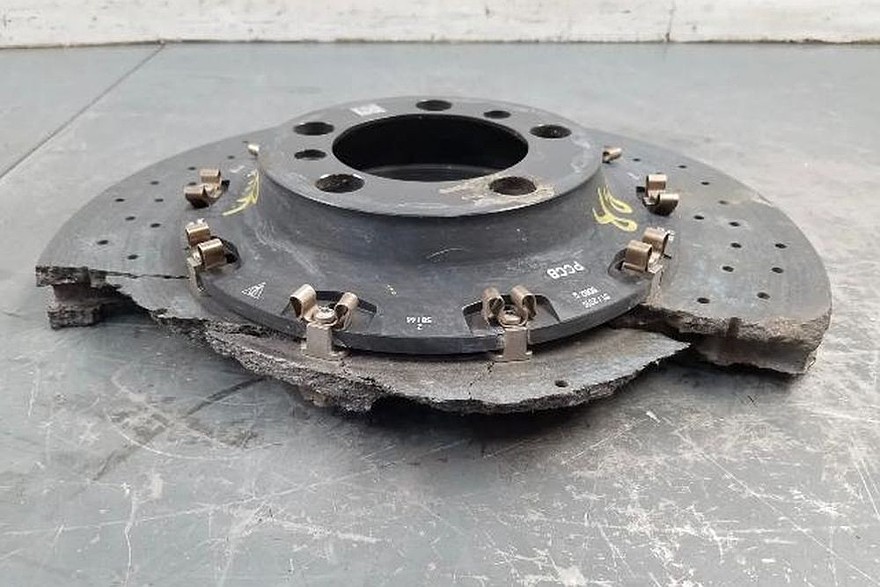
В настоящее время керамические тормозные диски производят лишь несколько компаний. Например, Brembo, Carbon Ceramics Ltd и SGL Carbon. Каждая компания использует свои технологии и рецепты изготовления керамических дисков, но в целом они сходны. Для широкого круга автомобилистов эти диски по-прежнему недоступны в силу своей высокой стоимости. В отличие, кстати, от керамических колодок, которые все же можно купить за более-менее адекватные деньги на многие автомобили.